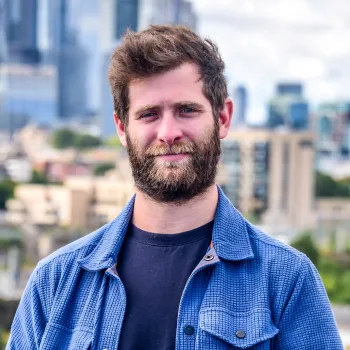
Alongside cost and energy, scale represents one of direct air capture’s (DAC) core existential battlegrounds. According to the world’s leading climate scientists, we are going to need gigatonne-scale carbon removal infrastructure in operation by 2050 — or a 100,000 scale-up of the amount of DAC capacity currently deployed across the world.
As an industry still in its infancy, switching from today’s first-of-a-kind deployments — which recover between 100-1,000-tonnes of atmospheric CO₂ a year — to delivering million-tonne-scale plants by 2030 requires pulling off some sort of process engineering magic trick.
DAC developers simply have to solve huge questions around their technologies’ design viability, manufacturing readiness, materials, and supply chain sustainability in a matter of years instead of decades.
Yet, solving the climate emergency requires this level of optimism. At Mission Zero Technologies, we believe that we have found a winning recipe for getting there — and the main ingredient is leveraging what already works.
What DAC can learn from the Gameboy
Before going any further, a moment of appreciation for the Gameboy — or, more specifically, its inventor Gunpei Yokoi, a seminal Nintendo product designer who helped to develop the product design philosophy critical to the Gameboy’s success.
Yokoi pioneered the idea of using ‘seasoned’ technologies (or, as the direct Japanese to English translation goes, ‘withered’ technologies) in new ways; essentially repurposing components and processes that had already been scaled to enable a new technology.
The Gameboy’s success wasn’t necessarily down to having cutting-edge games or graphics; its virality was largely due to delivering playability and functionality using computing technologies that were massively scaled instead of highly bespoke.
For Nintendo, the focus was on producing the highest quality product at the lowest cost, with a focus on scalability and mass production. This design philosophy has continued into Nintendo’s newer products, and the sales numbers speak for themselves: the Nintendo Switch was the quickest console in history to surpass 100M sales and Nintendo DS closely follows the PlayStation 2 as the second most popular console in history. Incidentally, third and fourth places are also both Nintendo products.
This represents a paradigm shift for technology development, where you traditionally start from somewhere off in the weeds of extreme ambiguity and slowly pay down your technical debt to reality by figuring things out and getting closer to certainty. By leveraging Yokoi’s wisdom, we can achieve something similar for DAC — starting from a much lower state of ambiguity.
Reducing technical risk using existing technologies
At Mission Zero we’ve done precisely this. Instead of developing bespoke new components, our DAC technology leverages off-the-shelf ones supported by global supply chains that have been proven across industry for decades. This allows us to skip a huge amount of technical risk, secure a clear pathway to mass manufacturing, and save literally decades of scaling work to deploy our systems.
And the proof is in deployment. Adopting this approach has enabled us to put three first-of-a-kind (FOAK) systems on the ground by our company’s fourth year of existence. The lessons we learn from each real-world deployment directly increase the speed, improve the efficiency, and decrease the cost of deploying further systems — all of which serves to de-risk our technology and accelerate our path towards larger-scale deployments.
It's a direct testament to Yokoi’s philosophy. We are minimising DAC technology and scaling risks at the same time by using decades worth of knowledge, literature, and human capital to inform our technology scoping process, aligned with specific market needs. By using well-understood and already scaled technologies in new ways, we can realise critical climate technologies faster.
The mature technologies inside a Mission Zero DAC plant
We have developed a breakthrough electrochemical direct air capture technology that repurposes componentry used widely across air handling and solution treatment industries, spanning indoor farming through to soy sauce and wine production. Crucially, all three of our FOAK systems have sourced these core components through different global suppliers without incurring dramatic cost, performance, or time implications.
Here’s a quick spotlight on the core mature tech that forms the backbone our first DAC systems.
Fans and sensors
We capture atmospheric CO₂ using the same designs, materials, processes, and supply chain as active cooling towers, which as a technology have been proven in industry for over 100 years.
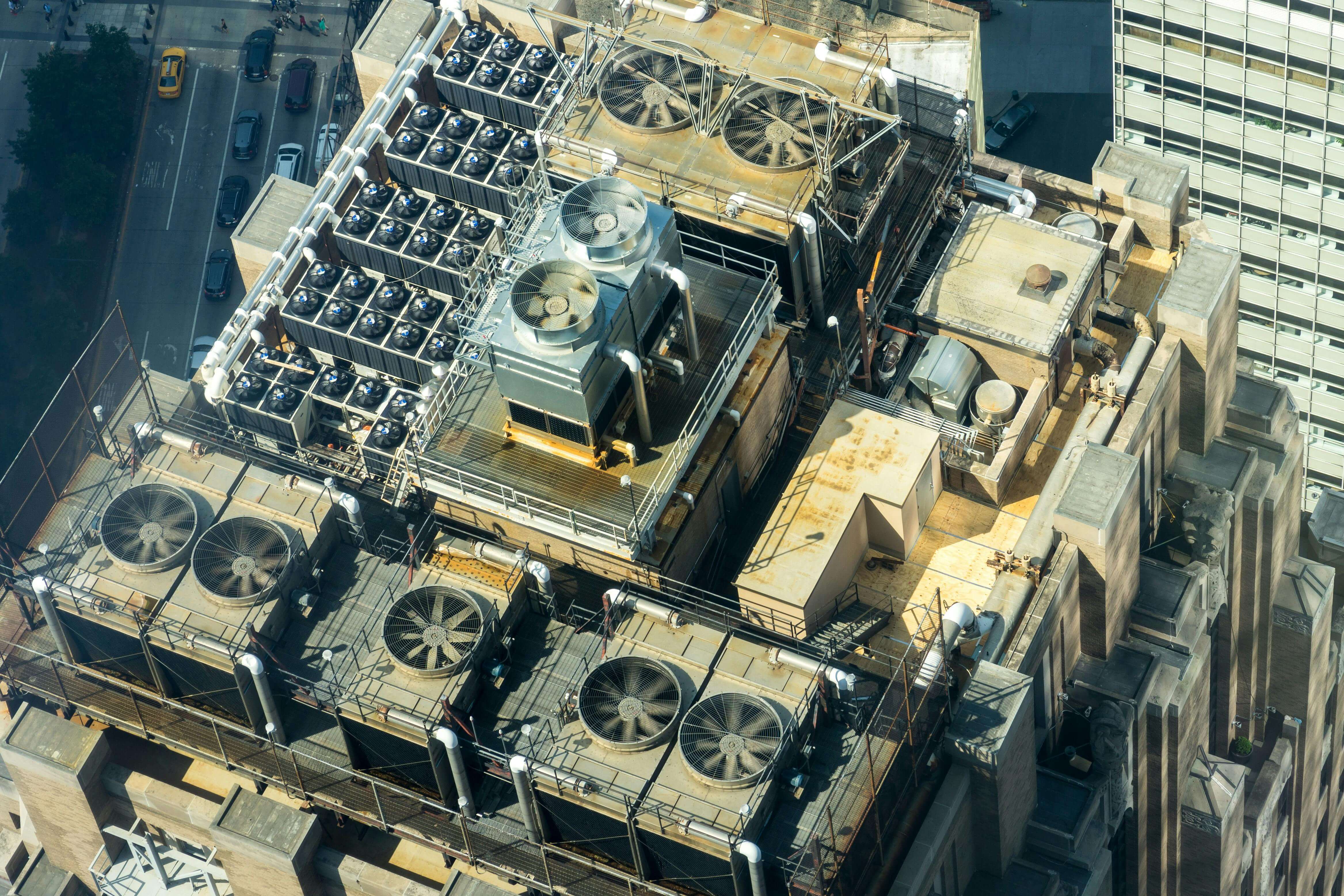
Electrodialysis stacks
We regenerate captured CO₂ using the same designs, materials, processes and supply chain as electrodialysis stacks, which have been used in industry for approximately 70 years.
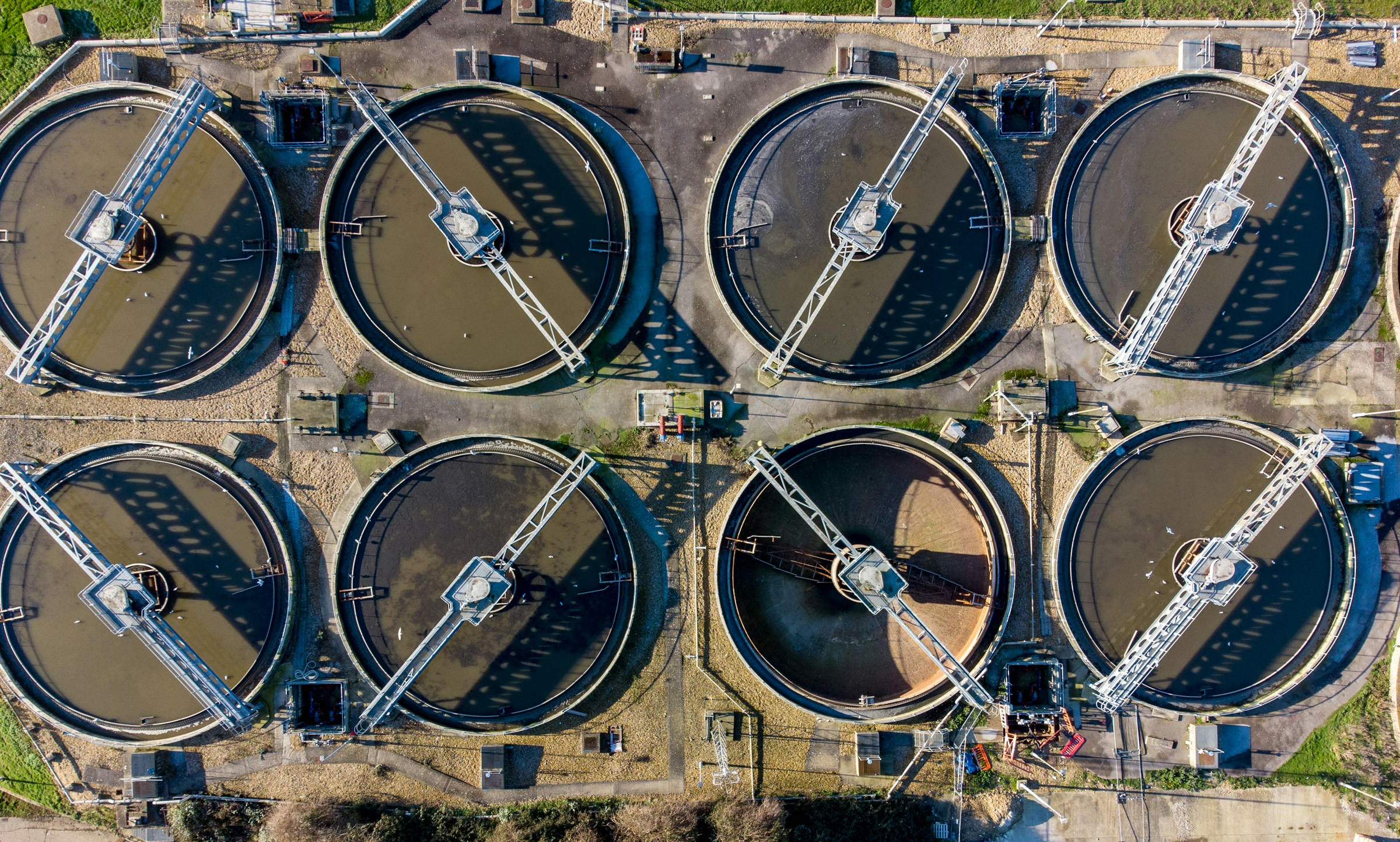
Ion-exchange membranes
We use scaled membranes that are widely used for desalinating sea water, demineralising whey, pickling bath recycling, stabilising wine, and recovering lithium.
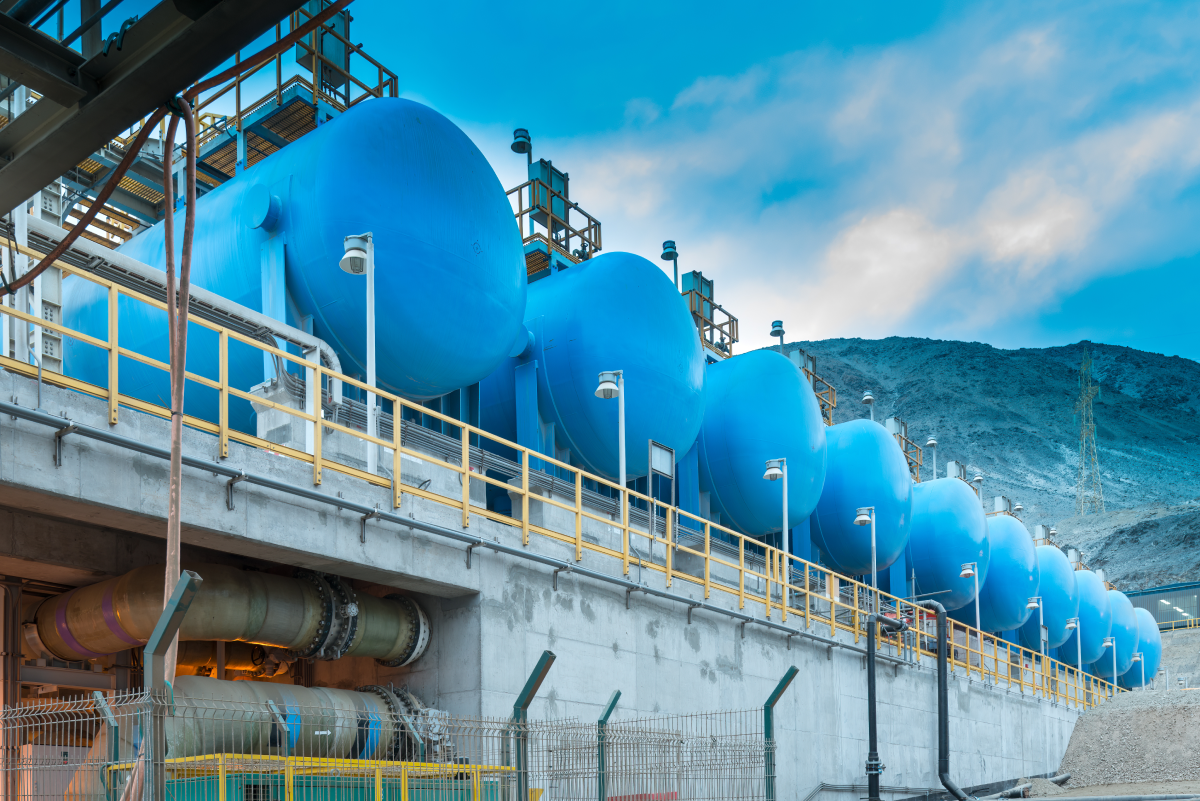
Shipping containers
Our systems are housed in ubiquitous 20- and 40-foot standard dry containers for easy modularity, customisation, global manufacture, and transportation.
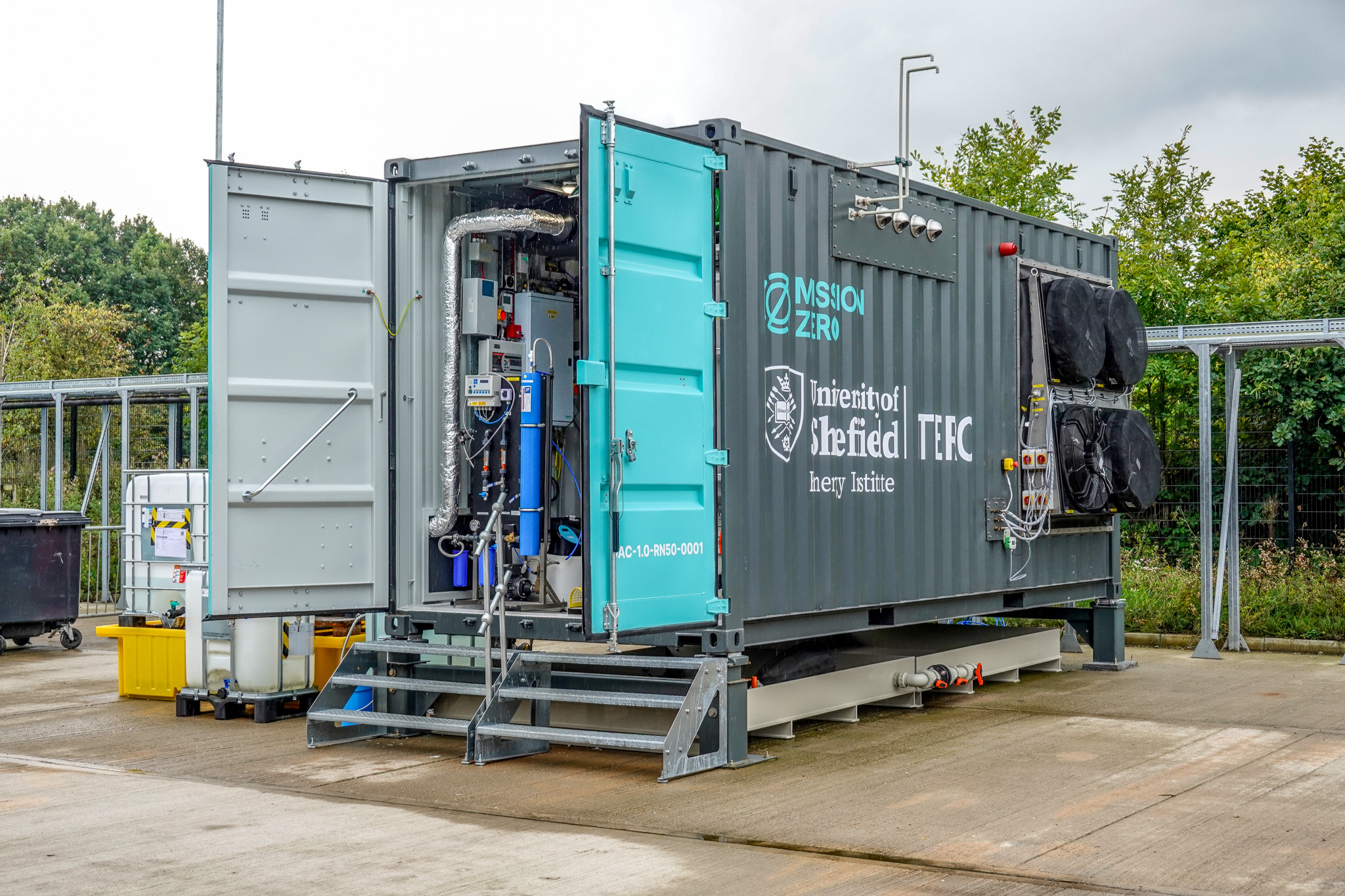
The bottom line on scaling DAC quickly
- We see that many DAC innovators are choosing to create highly bespoke components, but we believe that this will create a huge bottleneck for scaling in the future.
- Instead, at Mission Zero we leverage off-the-shelf technologies that have been proven in scaled industries for decades backed by mature supply chains.
- This approach has enabled us to rapidly put three DAC systems on the ground, while baking technical maturity into our systems and raising the manufacturing readiness level of our technology.
- Quick deployment is, in turn, enabling us to quickly acquire the real-world performance data required to rapidly learn, innovate, and secure early financial confidence in our technology.
- Gameboy is the gift that keeps on giving.
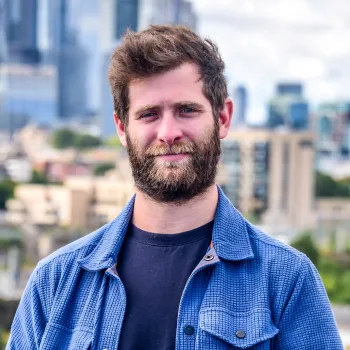
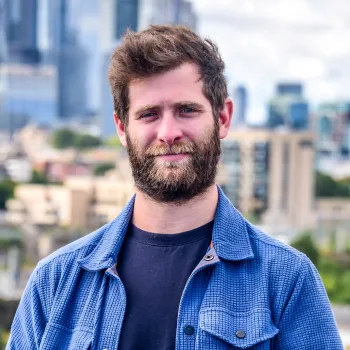