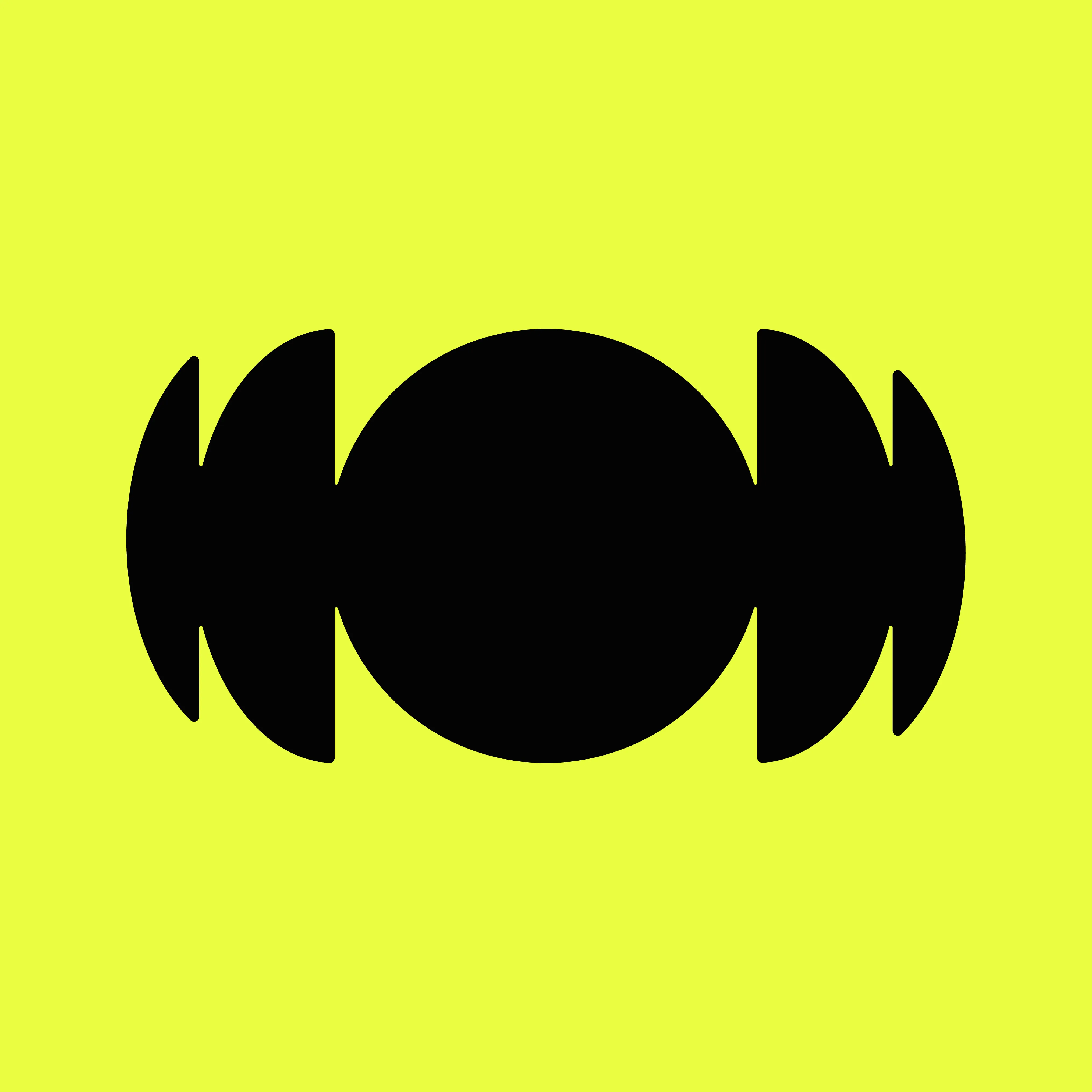
Direct air capture technologies all share the same goal: to recover carbon dioxide (CO₂) from the atmosphere as effectively as possible. Yet, scientifically speaking, there are hundreds of different ways to go about it.
Over the past few years, technological innovation within direct air capture has exploded. Globally, there are now well over 100 different direct air capture companies, with approximately 130 large-scale DAC facilities at various stages of development, and around 30 DAC plants commissioned to date — including our own first-of-a-kind DAC system in the UK.
All of this creativity is exciting; we are witnessing the birth of a global DAC industry. Yet, it’s also extremely confusing — especially for early adopters looking to understand the most effective and scalable carbon dioxide removal technology for the future. All this diversity makes it extremely hard to make a like-for-like comparison between different DAC methods.
As DAC developers, at Mission Zero we believe this is actually a good thing. Different DAC technologies hold their own unique situational advantages based on things like the climate, existing infrastructure, and geology of a given location. Here’s our attempt to break down the key differences between the most established methods out there.
How direct air capture technologies work
Before jumping into the main differences between direct air capture methods, you first need to understand the key battlegrounds of innovation that they all share.
All direct air capture technologies innovate across two core processes or ‘phases’:
- CO₂ capture: where CO₂ from the air is selectively bound to the capture medium (leaving behind other molecules).
- CO₂ regeneration: where bound CO₂ is released from the capture medium as a pure gas.
Differences across these processes mean that different direct air capture methods offer different profiles in terms of uptime, energy efficiency, mass deployability, materials efficiency, carbon intensity, ease of integration of CO₂ supply (for either utilisation or mineralisation), CO₂ purity, minimal servicing and maintenance requirements, and system simplicity — all of which impact a DAC technology’s overall cost and ability to scale.
CO₂ capture: The main differences within carbon removal tech
When a DAC system is flooded with air, the CO₂ contained within needs to be isolated and extracted, stripping it from the atmosphere.
Most direct air capture technologies follow one of two high-level approaches here: solid capture and liquid capture. Here’s what they mean.
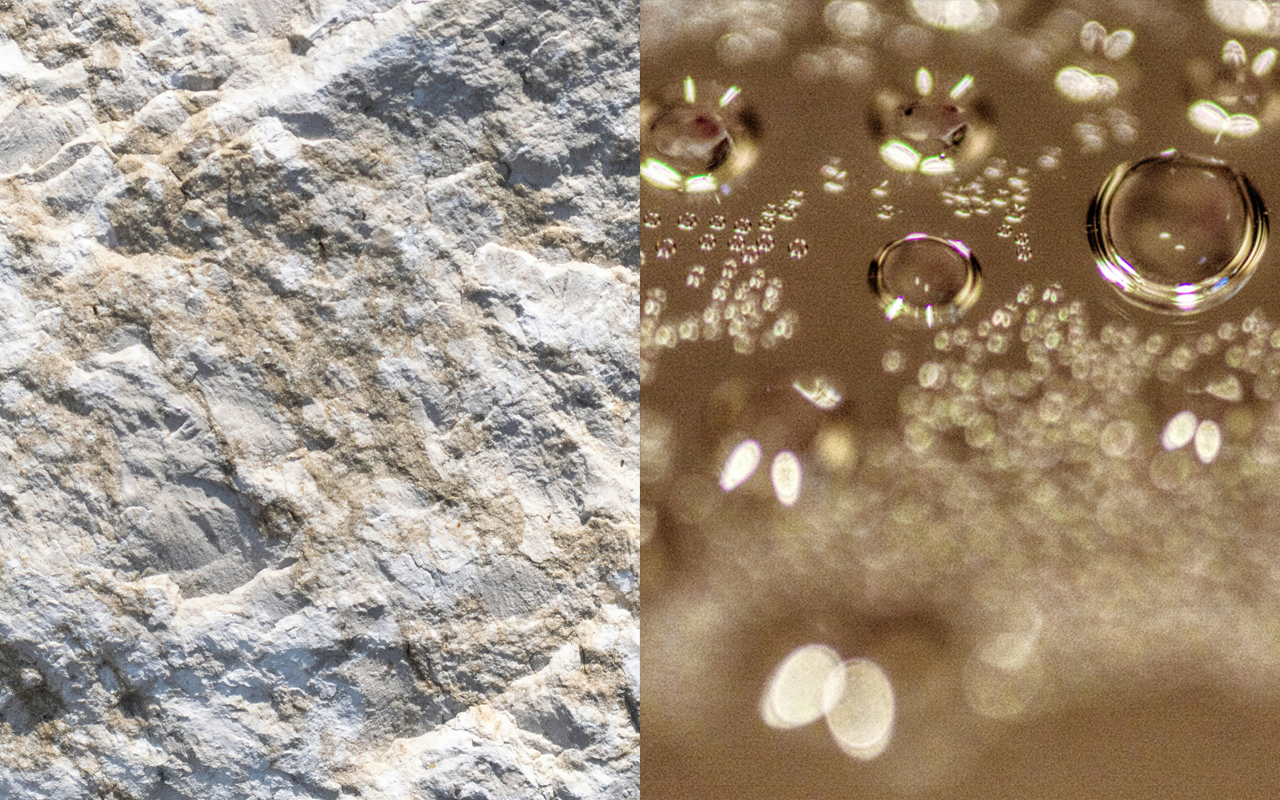
Solid capture
How it works: A solid sorbent (an insoluble material) adsorbs CO₂ from the air (the carbon particles in air stick to its surface).
Pros:
- High CO₂ selectivity: Sorbents can be highly selective for CO₂, reducing the capture of other gases and improving efficiency
- Reusability: Sorbents can often be regenerated and reused multiple times, making them cost-effective over time
- Stability: Sorbents are generally stable and have a long operational lifespan
Cons:
- Energy-intensive regeneration: Regenerating sorbents usually requires significant energy input, often involving high temperatures or vacuum conditions
- Complexity: Handling and maintaining sorbent systems can be complex and require sophisticated engineering solutions
- Capacity limitations: Sorbents may have lower CO₂ capture capacities compared to some liquid sorbents, necessitating frequent regeneration
Liquid capture
How it works: Liquid solvents absorb CO₂ from the air. The CO₂ dissolves into the liquid, forming a chemical bond.
Pros:
- Lower energy requirements: Regenerating solvents generally requires less energy compared to sorbents, often involving lower temperatures.
- High capacity: Solvents can absorb large quantities of CO₂, reducing the frequency of regeneration cycles.
- Simple handling: Solvents are easier to handle and can be pumped and processed with existing liquid handling infrastructure.
Cons:
- Corrosion or degradation: Solvents can be corrosive and may degrade over time, requiring replacement or treatment.
- Evaporation losses: Some solvents may experience evaporation losses, increasing operational requirements.
CO₂ regeneration: DAC’s biggest site for difference
Things get most interesting in the third and final part of the process — CO₂ regeneration. This is where the CO₂ is released from the capture medium and also happens to be the phase where you can see the biggest differences across cost and efficiency.
Regeneration can be broken down into the following four main areas.
Low-grade heat (<200°C)
Low-grade heat regeneration involves heating the loaded capture medium to a temperature below 200°C to release CO₂. This method is typically used with solvents or certain sorbents that desorb CO₂ at lower temperatures.
Whilst low-grade heat requires less energy than high-grade processes to release carbon, desorption can be slower and working at lower temperatures can sometimes decrease the capture capacity of certain capture mediums.
This method is favoured by the ‘first generation’ of direct air capture technologies, including Climeworks and Global Thermostat.
High-grade heat (~800°C)
High-grade heat regeneration requires heating the capture medium to temperatures of around 800°C, and is typically used for solid sorbents like metal oxides.
This method comes with high efficiency, but calls for significant energy usage, which can be problematic when it comes to keeping costs low, or if fossil-based energy is used to power the process. Integrating renewable energy sources into direct air capture technology is vital to overcoming this. Repeated high-temperature cycles can also degrade capture materials over time.
DAC players including Carbon Engineering and Heirloom use high grade heat in their carbon removal tech.
Humidity
Humidity-based regeneration exposes capture mediums to moisture, which can help release the captured CO₂ through a process called moisture swing adsorption (the swing part just means a change from one state of humidity to another, e.g. dry to wet and back).
Humidity as a direct air capture release method requires minimal energy and is a relatively simple process, albeit, a slower one than thermal methods.
Companies including Avnos and Mechanical Trees are fans of this approach, which is used to power their carbon dioxide removal technology.
Electrochemical
Our chosen approach — electrochemical regeneration uses an electric current to induce chemical reactions that release the captured CO₂ from the capture medium.
As a heat-free, entirely electrified process, this method can be powered entirely by renewable energy. It offers one of the lowest carbon footprints and highest energy efficiencies of all direct air capture technologies.
By leveraging widely-available existing electrochemical technologies that are commonly used across industry, electrochemical direct air capture also has the ability to scale quickly.
Dive deeper: see what the electrochemical DAC's energy flexibility advantage means for bringing down costs.
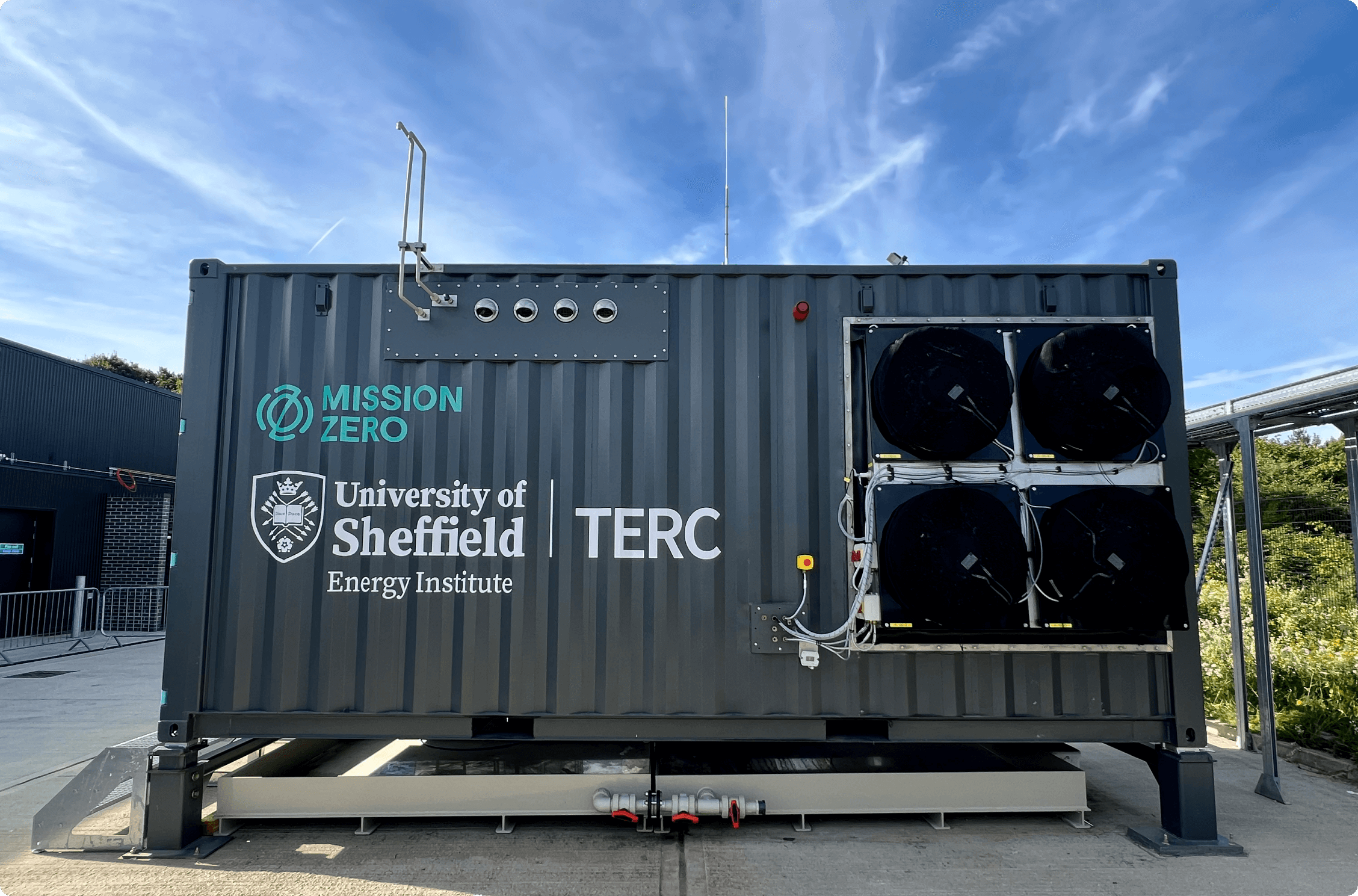
Diversity in direct air capture technologies is a good thing
One-size-fits-all direct air capture technology is neither thermodynamically possible or commercially desirable. All of the process differences we’ve explored above can hold specific benefits and drawbacks depending on the location of a specific deployment.
A few examples of how different DAC technologies play to the strengths of different environments:
- Heat-based: A good choice for sites where geothermal or waste heat from an existing energy system is readily available, or in cold climates where a heated system protects against freezing
- Moisture swing: Suited to water-scarce areas, since little to no water is used in the process
- Electrochemical: Ideal for areas with access to cheap and/or intermittent renewable power due to its inherent energy flexibility
Ultimately, the best direct air capture technology will be the one that best suits the unique needs of a given project. To understand precisely what different DAC technologies offer to maximise their climate mitigation potential, we need as many of them to be deployed and tested in real-world settings as quickly as possible.
💡 Learn more about our direct air capture projects
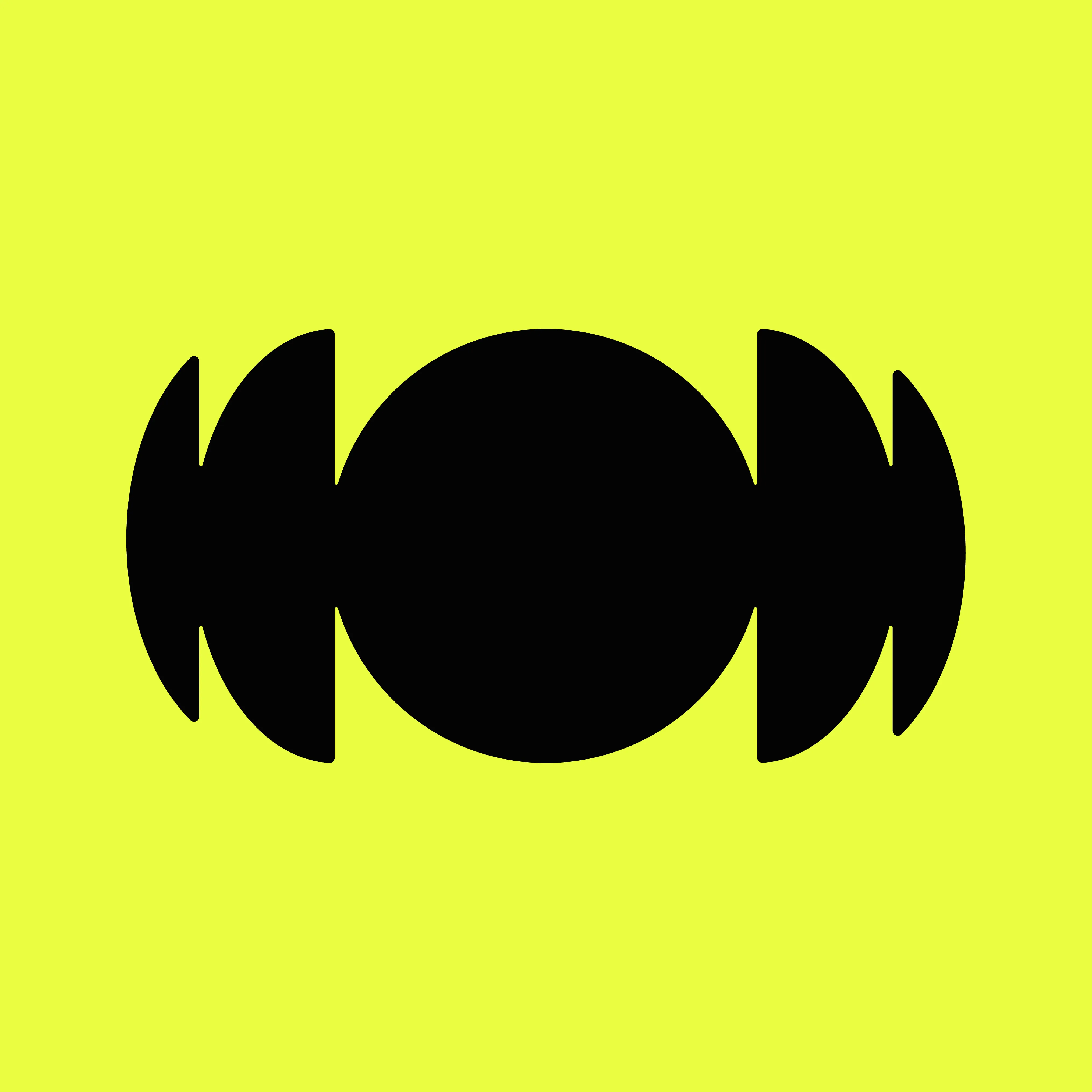
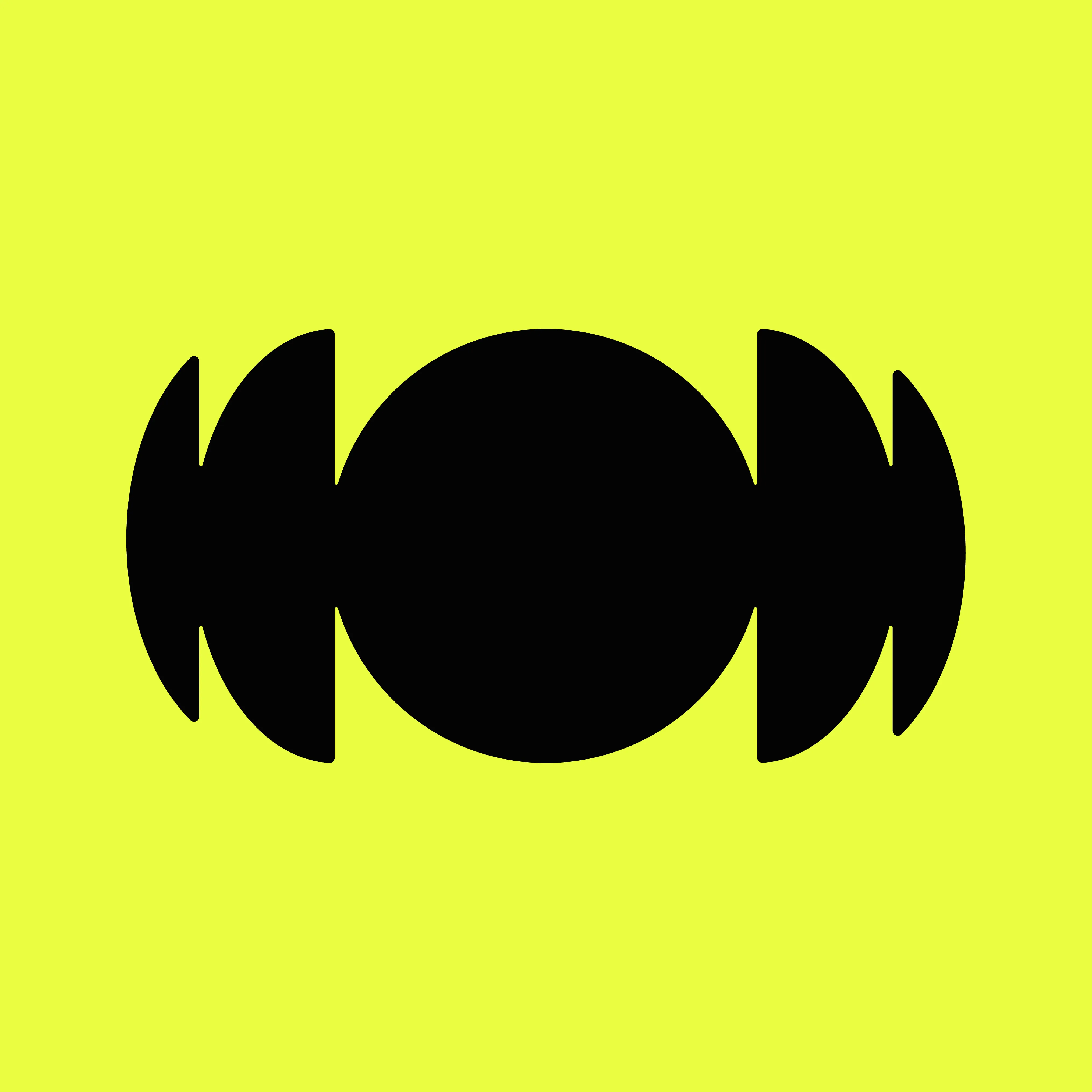